How Model Inaccuracy or Incompleteness Inhibits Contractors from Implementing 4D and 5D BIM
- Loyiso Toyi
- Mar 25
- 5 min read
Updated: Apr 12
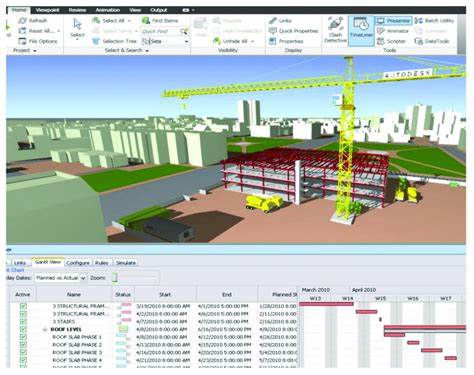
Building Information Modeling (BIM) has revolutionized the construction industry by enabling better planning, coordination, and execution of projects. Among its advanced applications, 4D BIM (time/scheduling) and 5D BIM (cost estimation) have emerged as powerful tools for improving project efficiency and control. However, the effectiveness of these tools heavily depends on the accuracy and completeness of the underlying 3D model. When models are inaccurate or incomplete, contractors face significant challenges in implementing 4D and 5D BIM, leading to delays, cost overruns, and inefficiencies.
We will explore how model inaccuracy, or incompleteness impacts 4D and 5D BIM implementation, the root causes of these issues, and strategies to mitigate them.
The Role of 4D and 5D BIM in Construction
Before diving into the challenges, let’s briefly understand what 4D and 5D BIM bring to the table:
4D BIM (Time/Scheduling): This integrates the 3D model with the project schedule, allowing stakeholders to visualize the construction sequence over time. It helps in identifying potential delays, optimizing workflows, and improving communication.
5D BIM (Cost Estimation): This adds cost data to the 3D model, enabling accurate quantity takeoffs, cost estimation, and budget tracking throughout the project lifecycle.
Both 4D and 5D BIM rely on a robust and accurate 3D model to function effectively. When the model is flawed, the entire process breaks down.
How Model Inaccuracy or Incompleteness Impacts 4D and 5D BIM
Challenges in 4D BIM Implementation
Inaccurate Sequencing
A flawed model can lead to incorrect sequencing of construction activities. For example, if a structural element is missing from the model, the schedule might not account for its installation, causing delays and rework.
Contractors rely on 4D BIM to plan the order of tasks. Inaccurate models disrupt this planning, leading to inefficiencies on-site.
Unreliable Visualization
4D BIM is used to visualize the construction process over time. If the model is incomplete, the visualization may omit critical components, leading to misunderstandings and miscommunication among stakeholders.
For instance, missing MEP (mechanical, electrical, plumbing) elements in the model can result in unrealistic timelines, as their installation is not accounted for.
Clash Detection Issues
One of the key benefits of 4D BIM is its ability to detect clashes early in the planning phase. However, an incomplete model may miss critical clashes, leading to costly delays and rework during construction.
For example, if a ductwork clash is not detected in the model, it may only be discovered on-site, requiring redesign and delaying the project.
Difficulty in Progress Tracking
Contractors use 4D BIM to track progress against the schedule. If the model is incomplete, it becomes challenging to compare actual progress with the planned schedule, reducing the effectiveness of progress monitoring.
Missing elements in the model can lead to inaccurate progress reports, making it difficult to identify delays and take corrective action.
Challenges in 5D BIM Implementation
Inaccurate Quantity Takeoffs
5D BIM relies on accurate quantity takeoffs from the 3D model to estimate costs. If the model is incomplete or inaccurate, the quantities derived will be incorrect, leading to unreliable cost estimates.
For example, missing walls or structural elements in the model can result in underestimating material quantities, leading to budget overruns.
Cost Overruns
Inaccurate models can result in underestimating or overestimating material quantities, labor, and equipment requirements. This can lead to budget overruns or underutilization of resources, impacting project profitability.
For instance, if the model does not accurately represent the complexity of a structural component, the cost estimate may not account for the additional labor and materials required.
Difficulty in Cost Forecasting
5D BIM is used to forecast costs throughout the project lifecycle. Inaccurate models make it difficult to predict future costs accurately, reducing the ability to manage budgets effectively.
Missing elements in the model can lead to unexpected costs during construction, as they were not accounted for in the initial estimate.
Integration Issues
5D BIM requires integration with cost databases and estimation tools. Incomplete models can lead to gaps in data integration, making it harder to generate accurate cost reports and forecasts.
For example, if the model does not include all necessary components, the cost estimation software may not be able to generate a comprehensive cost report.
General Impacts on BIM Implementation
Reduced Collaboration
Inaccurate or incomplete models hinder collaboration among stakeholders, as they cannot rely on the model for decision-making. This undermines the collaborative nature of BIM.
For instance, if the architect and contractor are working with different versions of the model, it can lead to miscommunication and errors.
Increased Rework
Errors in the model often lead to rework during construction, which increases costs and delays the project. This negates the benefits of using 4D and 5D BIM for planning and cost control.
For example, if a structural element is missing from the model, it may need to be redesigned and reinstalled, leading to delays and additional costs.
Loss of Trust
If contractors consistently encounter inaccuracies in the model, they may lose trust in the BIM process, leading to reduced adoption and reliance on traditional methods.
For instance, if a contractor repeatedly encounters errors in the model, they may choose to rely on 2D drawings instead, reducing the effectiveness of BIM.
Inefficient Resource Allocation
Inaccurate models can lead to poor resource allocation, as contractors may over-order or under-order materials, or misallocate labor and equipment.
For example, if the model does not accurately represent the quantity of materials required, the contractor may order too much or too little, leading to waste or delays.
Strategies to Overcome Model Inaccuracy and Incompleteness
To ensure that 4D and 5D BIM processes run smoothly, contractors and project teams must take proactive steps to improve model accuracy and completeness. Here are some key strategies:
Early Collaboration
Encourage early and continuous collaboration among all stakeholders to ensure the model is accurate and complete.
Utilize Information Delivery Specification (IDS) to ensure that all required data is included at each project stage.
Model Audits
Conduct regular model audits to identify and rectify inaccuracies or missing elements before they impact 4D and 5D BIM processes.
Training and Standards
Provide training for team members on BIM standards and best practices to minimize errors and improve model quality.
Ensure that model elements contain necessary parameters for scheduling and cost estimation.
Encourage knowledge sharing through lessons learned from past projects.
Use of Clash Detection Tools
Implement clash detection tools during the design phase to identify and resolve conflicts early, ensuring a more accurate model.
Leverage BIM Execution Plans (BEP)
Develop a detailed BEP that outlines roles, responsibilities, and processes for model creation and maintenance.
Conclusion
Model inaccuracy or incompleteness is a significant barrier to the successful implementation of 4D and 5D BIM. It undermines the reliability of scheduling, cost estimation, and overall project control, leading to delays, cost overruns, and inefficiencies. By addressing the root causes of these issues and adopting best practices, contractors can unlock the full potential of 4D and 5D BIM, leading to more efficient and successful projects.
As the construction industry continues to embrace digital transformation, ensuring the accuracy and completeness of BIM models will be critical to realizing the benefits of advanced BIM applications. Let’s build smarter, not harder!
Comentarios